Produced and Frac Water Treatment
Experience
We treat oil and gas
wastewater from the
Bakken to the Eagle Ford.
WSI can build custom equipment for any oil and gas operations. Our entire engineering team has personally worked, designed and operated at energy sites around the world.
Our systems are reliable and have an unbeatable track record for effluent quality and reuse. They can be remotely controlled and operated with minimal supervision.
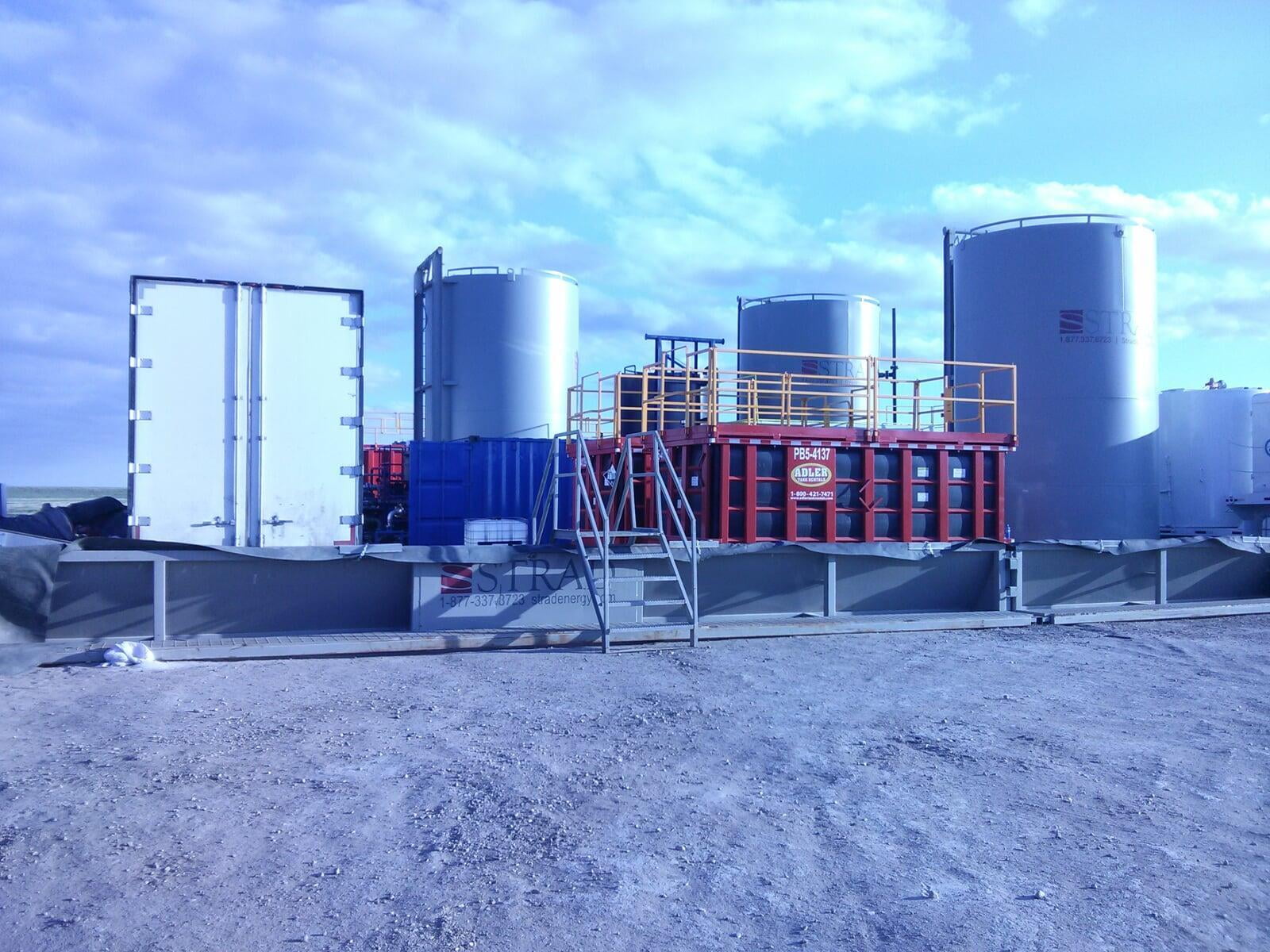
Temporary Sites
WSI's equipment has been designed on skids and trailers to allow rapid deployment to the field. The modular units can be configured for site-specific requirements and assembled in under a week. All equipment is Class I Div II rated.
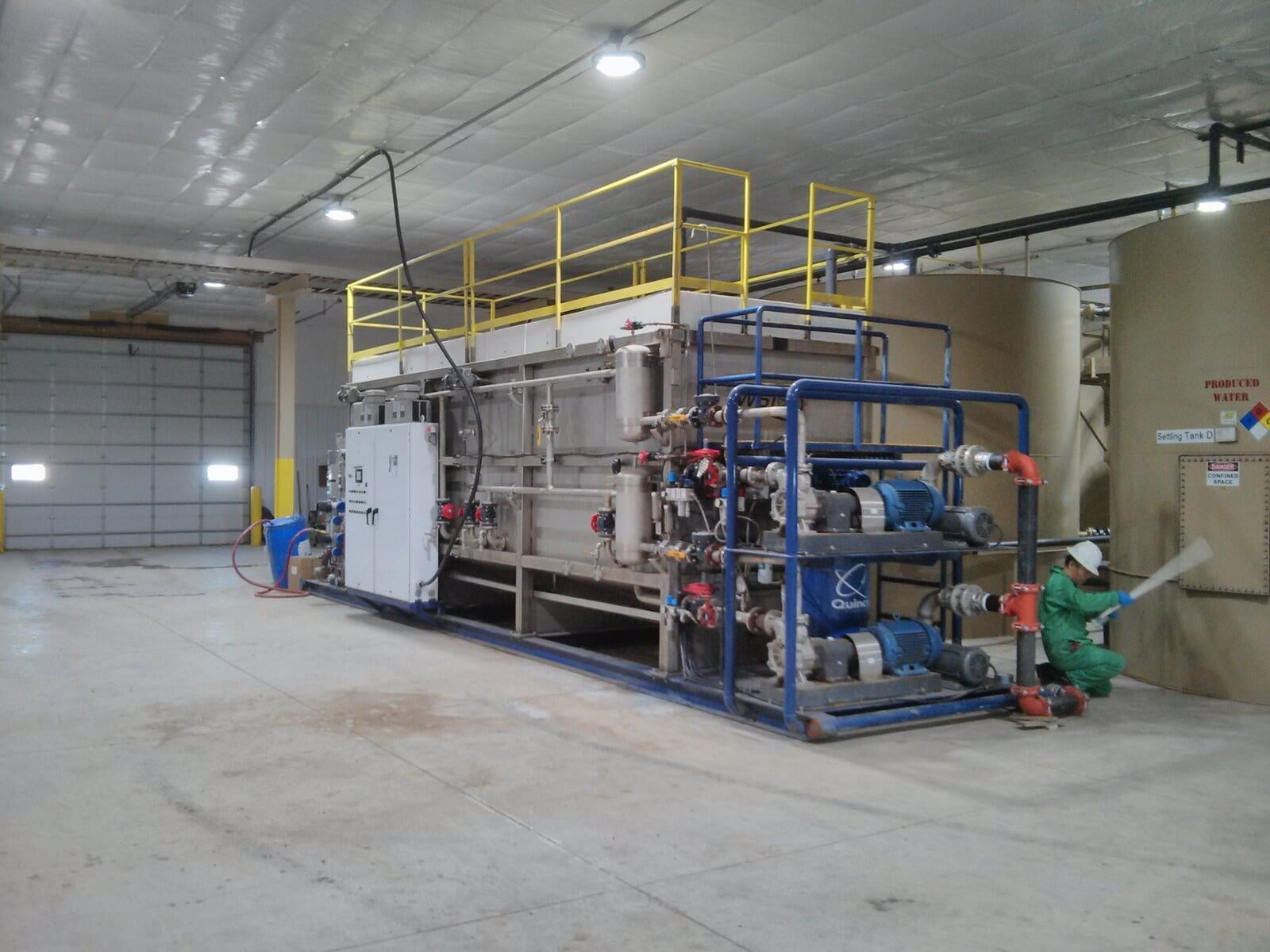
Fixed Installations
Our equipment has everything a new build or existing facility needs from controls to pumps. Our skids come prewired and ready for use when they arrive at the treatment facility. Each unit is thoroughly tested at our facility in Colorado.
Our Equipment
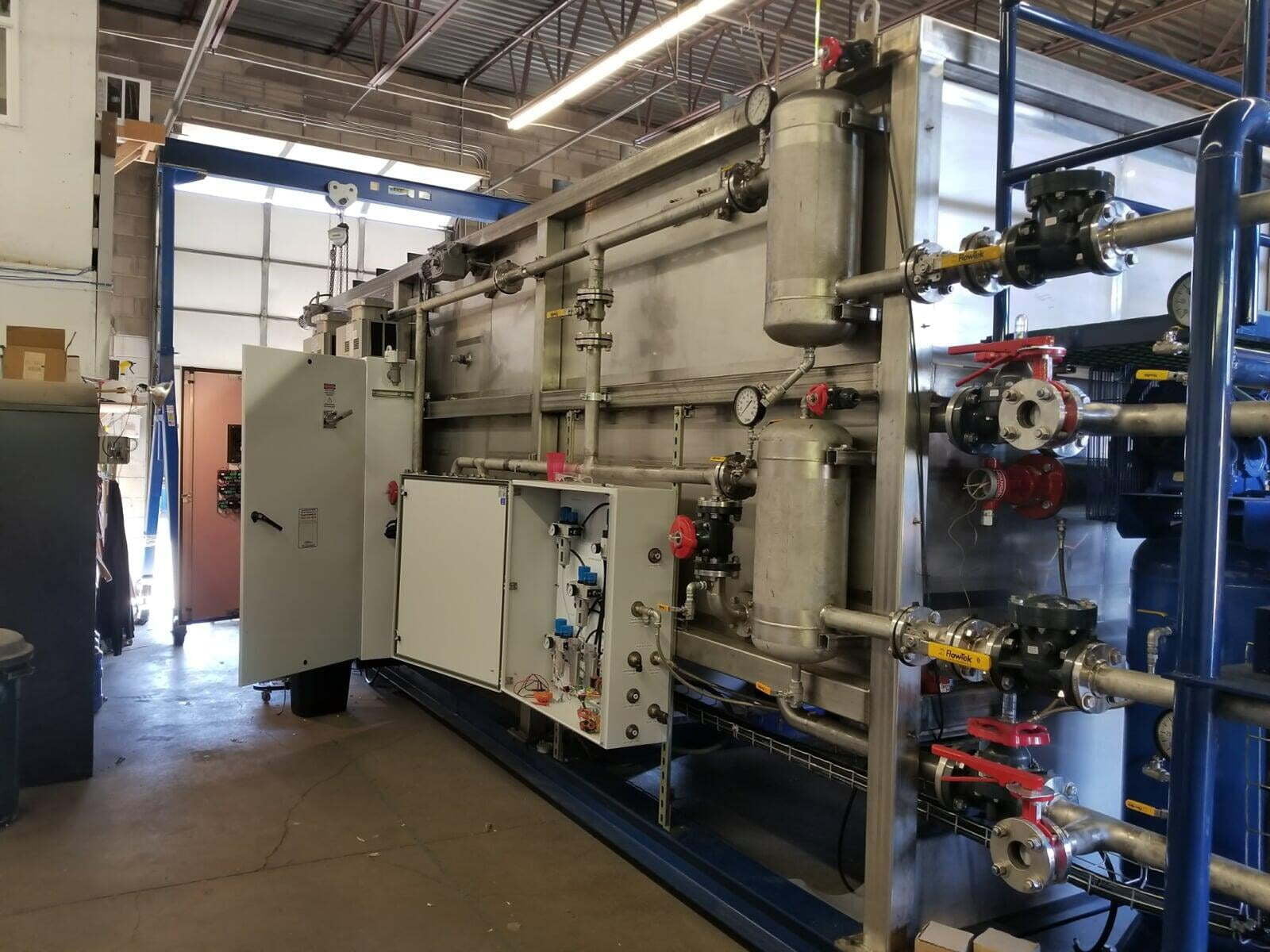
Dissolved Air Flotation (DAF)
Belt Press
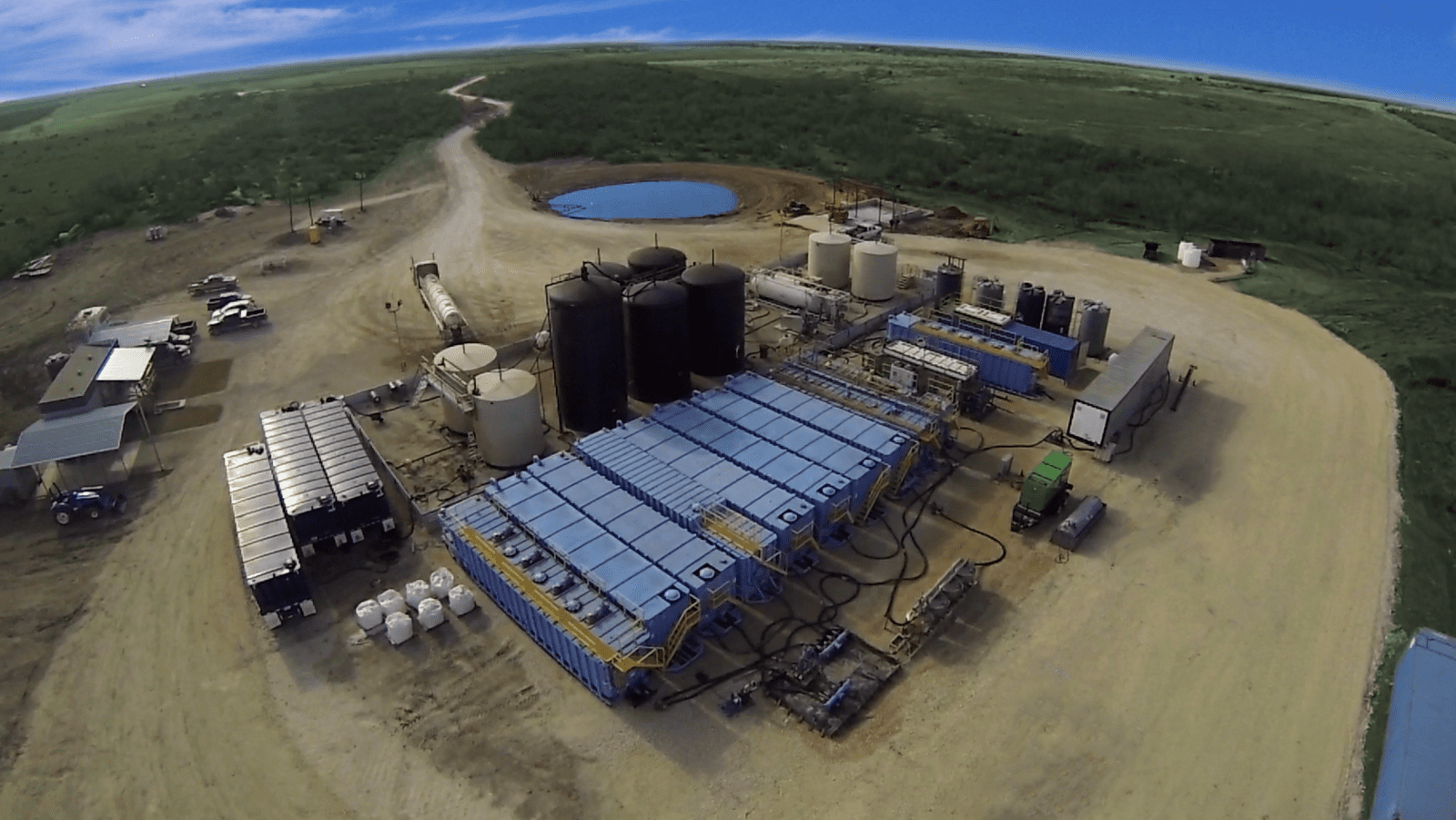
Mobile Modular Units
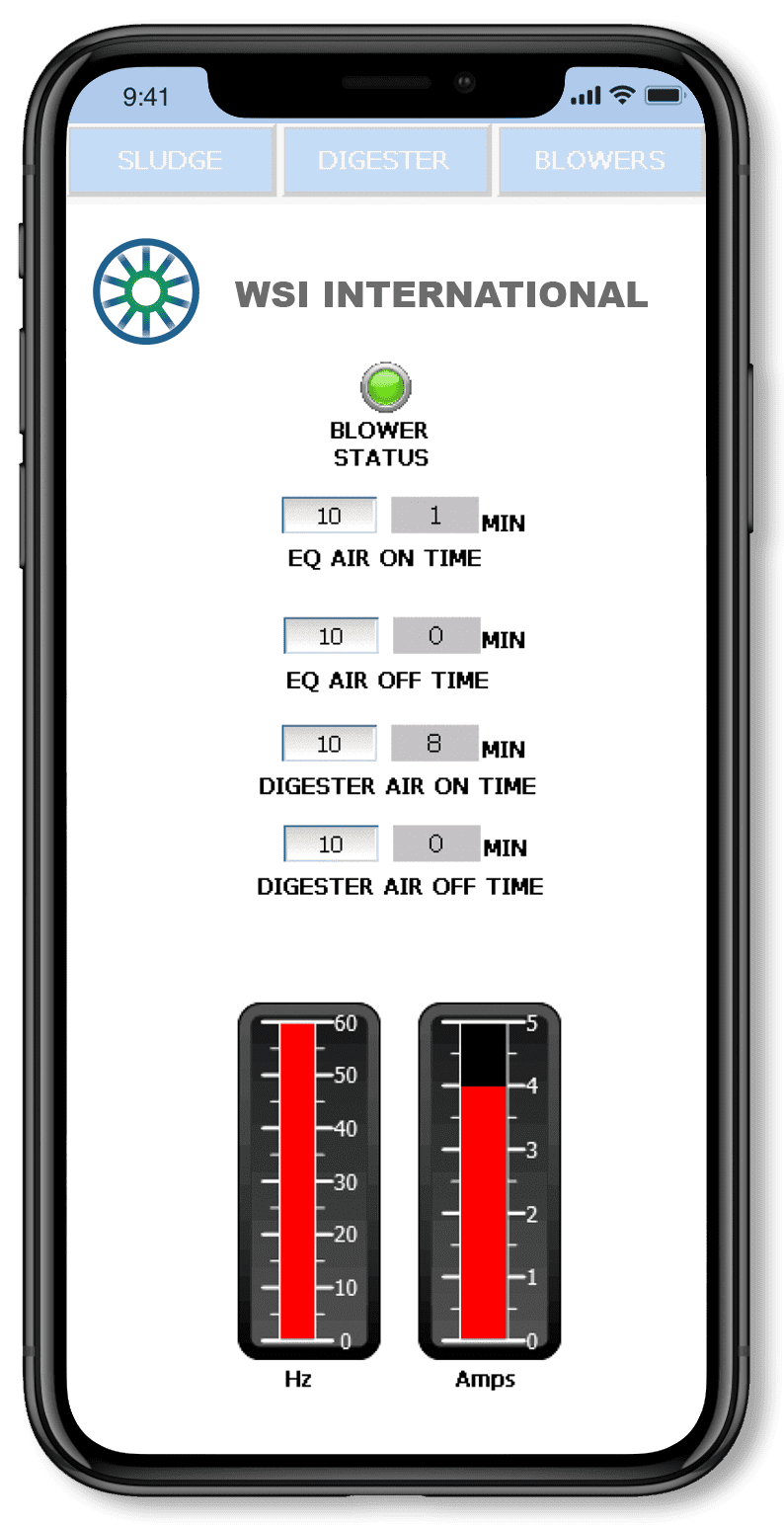
Our Process
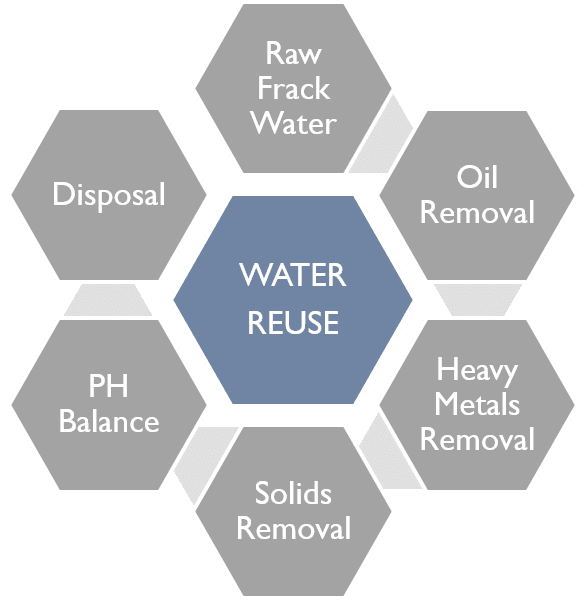
Custom Solutions for
Custom Problems
Each Oil and Gas wastewater stream is different and requires special analysis and expert scrutiny. Contact us and our team of environmental, mechanical and systems engineers will come up with a custom solution to your project.
Core Produced Water Treatment Technologies
Our Clients
We've worked with small local producers to international companies. We offer solutions that cover all budgets.
